It’s tough to be a retailer trying to open new stores right now. Everyone is experiencing high costs, lack of materials, logistical issues, and labor issues. One of the hot topics at the ICSC convention this year was the idea of layered construction. Layered construction allows the retailer to open sooner, albeit not in the ideal state. Layered construction is the outcome of more than two years of pandemic-related supply chain and labor shortage issues that show no real signs of letting up any time soon, which have only been exacerbated by the war in Ukraine.
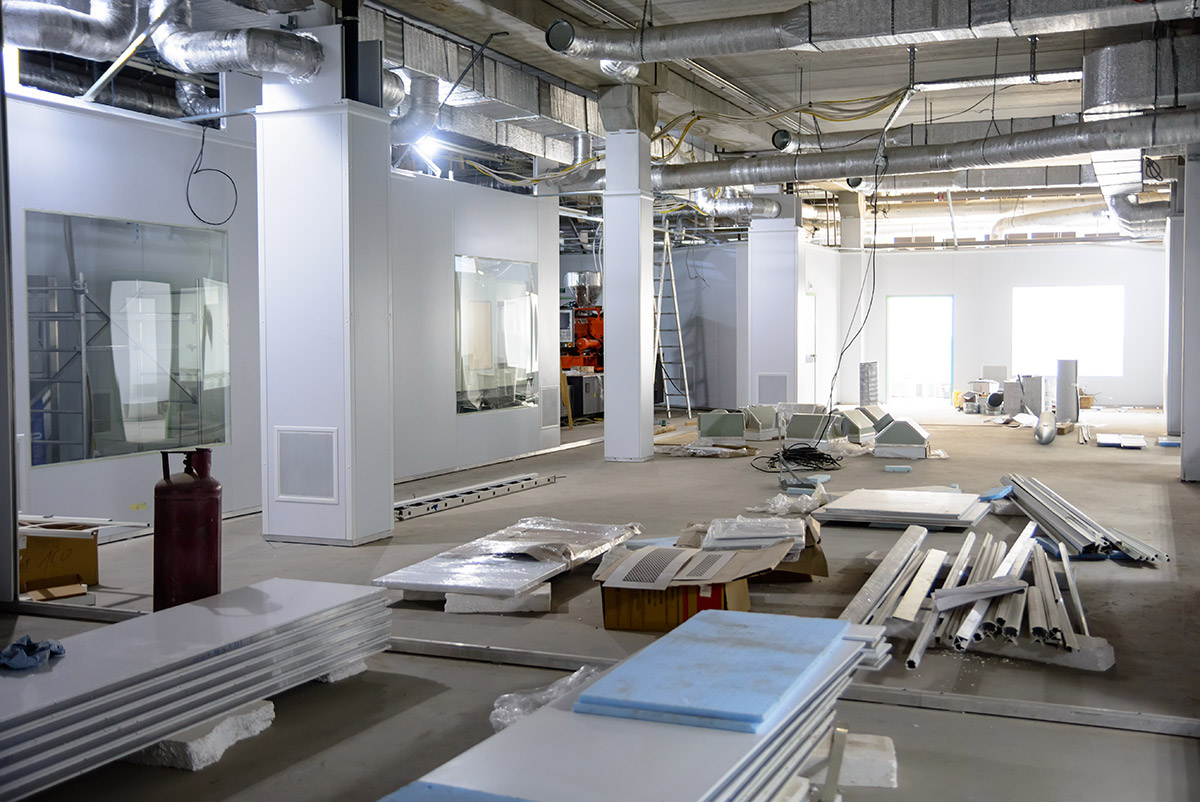
What Is Layered Construction?
Layered construction is an approach to launching a new location in the midst of all the construction industry challenges currently besetting the industry. It can take much too long for a brand to realize the ideal design for a new location due to shortages or wait times for materials, labor, and partner resources, so they sacrifice or alter the design to help facilitate progress towards opening. This can look like many things, but basically, it means implementing a new prototype in layers. For example, a store has a new, beautiful storefront design, but the design requires certain materials which are not accessible for 22 weeks, despite sourcing locally or looking for custom-made solutions. Waiting 22 weeks for the materials isn’t feasible when the store needs to be open for customers now, so the design is built in layers. Often, this means creating an alternative to the prototype that can be built immediately, then returning later to update with the correct materials when they’re finally available.
Drawbacks of Layered Construction
For retailers, the design of a location is a significant piece of the branding. By opening without having the design elements in place, they risk losing that all-important customer experience element that drives loyalty and return visits. However, this is the world everyone is living in right now. While it adds complexity to the construction and design build, it’s important to move forward, even though there may be a slower response to what should be a great store experience.
Even with these drawbacks, because labor and supply chain issues are having such a significant impact on construction schedules, retailers who want to open more quickly are using a layered construction approach to be able to open their doors to consumers even before the elements of their retail design are complete. It’s not a perfect solution, but when handled properly, it can be a way for retailers to more quickly.
Processed Have Changed
Processes have changed dramatically, and because most of these things are completely outside the control of the agency and the client, it becomes a matter of adjusting to the changes, communicating them effectively, and adjusting internal processes to accommodate the changes. For example, permit times have doubled in the last year.
“Speed is no one’s ally”
explains Liz Seitz, ASG’s Store Planning and Construction Leader. “What used to be a 6-8-week timeline, is now 20 weeks in some scenarios.” What agencies must do to help assuage the frustration for clients is to perform due diligence and organize everything prior to construction to make the process quicker and more efficient to execute.
Agencies must be vigilant, keeping their eye on the swiftly changing environment. “As soon as one lever opens up, another one, down the road we never expected, shuts,” says Seitz. Sometimes, Liz explains, it’s important pump the brakes earlier- talk to vendors and ensure construction schedule will align for everything to come along as scheduled.
“Companies will do anything to get into their space,” says Seitz. “They will literally rig their HVAC to make it into their space quicker.”
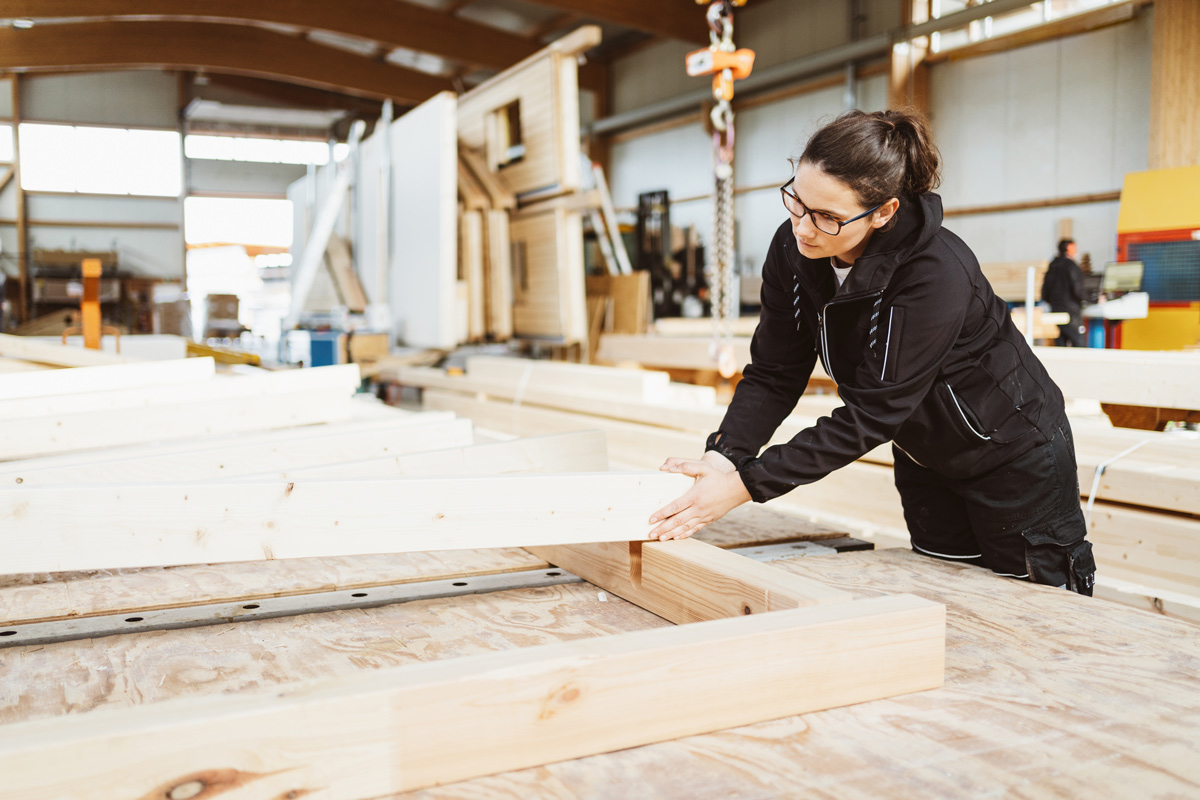
Globalization is Challenged
For years, the industry has relied on globalization as a solution that delivered cost-effective materials. Now, sourcing materials are part of the challenge. Could anyone have possibly predicted that just as we were coming out of the worst part of the global pandemic that a war would break out? Ukraine may be a small country, but it is pivotal politically and geographically for both food (Ukraine is a major wheat supplier) and oil (most of Europe imported oil from Russia and have stopped because of the invasion.
“None of us expected that after covid, another massive global crisis would emerge,” says Seitz.
Global struggles have a direct effect on US construction in some fashion, and all these factors make it more difficult to consider offshore manufacturing, at least in the short term. Complicating matters is that fewer and fewer people in America can actually put things together.
It’s the agency’s responsibility to have everything organized, to simplify the process and make the job simpler for vendors, contractors, and partners, but that’s far more difficult to do when everything is so much more unpredictable.
Supply Chain Woes
As with so many other industries, the construction industry has been plagued with supply chain issues. These issues are now compounded by a backlog of projects, a new infrastructure bill, and pent up demand for projects that were put on hold during the pandemic. These supply chain issues are impacting every phase of construction, and lead times are growing, exacerbated by the labor shortage in the trucking industry that moves the materials.
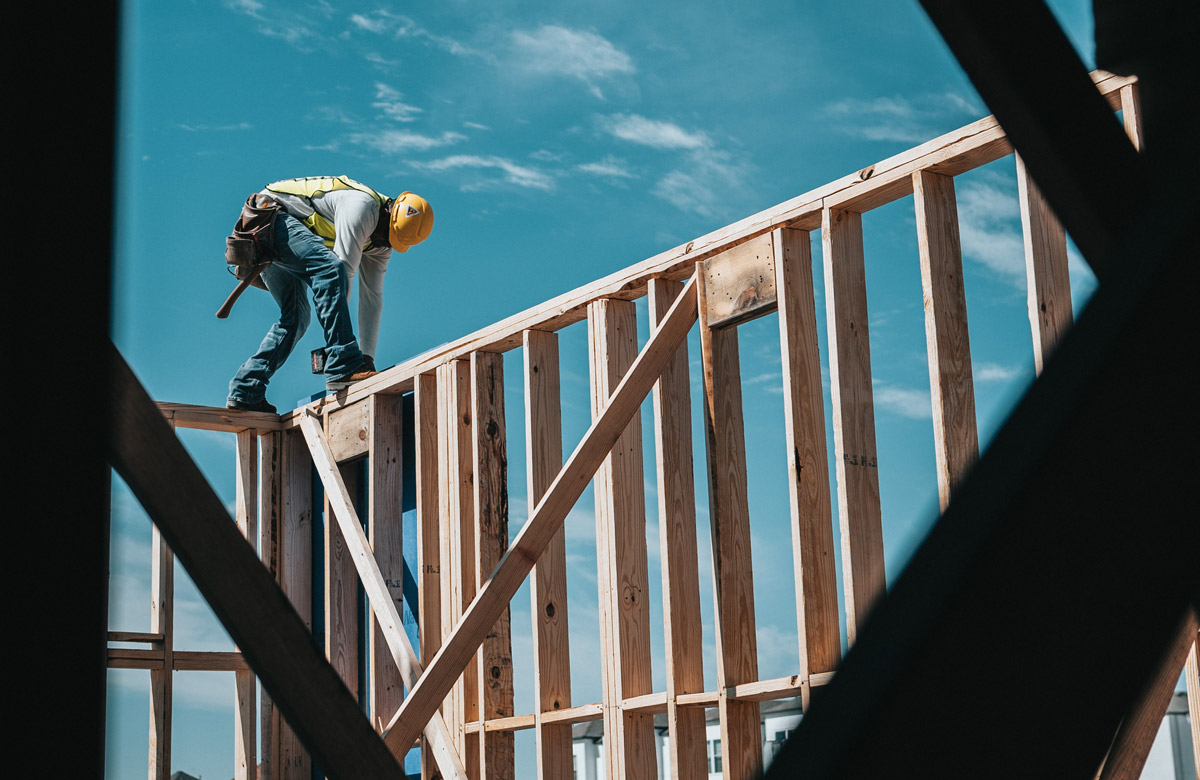
Labor Shortage
According to the Associated Builders and Contractors (ABC) organization, the construction industry needs 650,000 additional workers on top of the normal pace of hiring in 2022 to meet the demand for labor. In 2023, ABC says the industry will need to bring in nearly 590,000 new workers on top of normal hiring to meet industry demand. The labor shortage is compounded by a tattered supply chain. It’s not just that there are labor shortages in general. It’s that the labor shortages are hitting blue-collar jobs, so even when the store is finally able to get the materials, they may not be able to find enough people to do the work, whether it’s installing fixtures or painting, or specialized services like plumbing and electric.
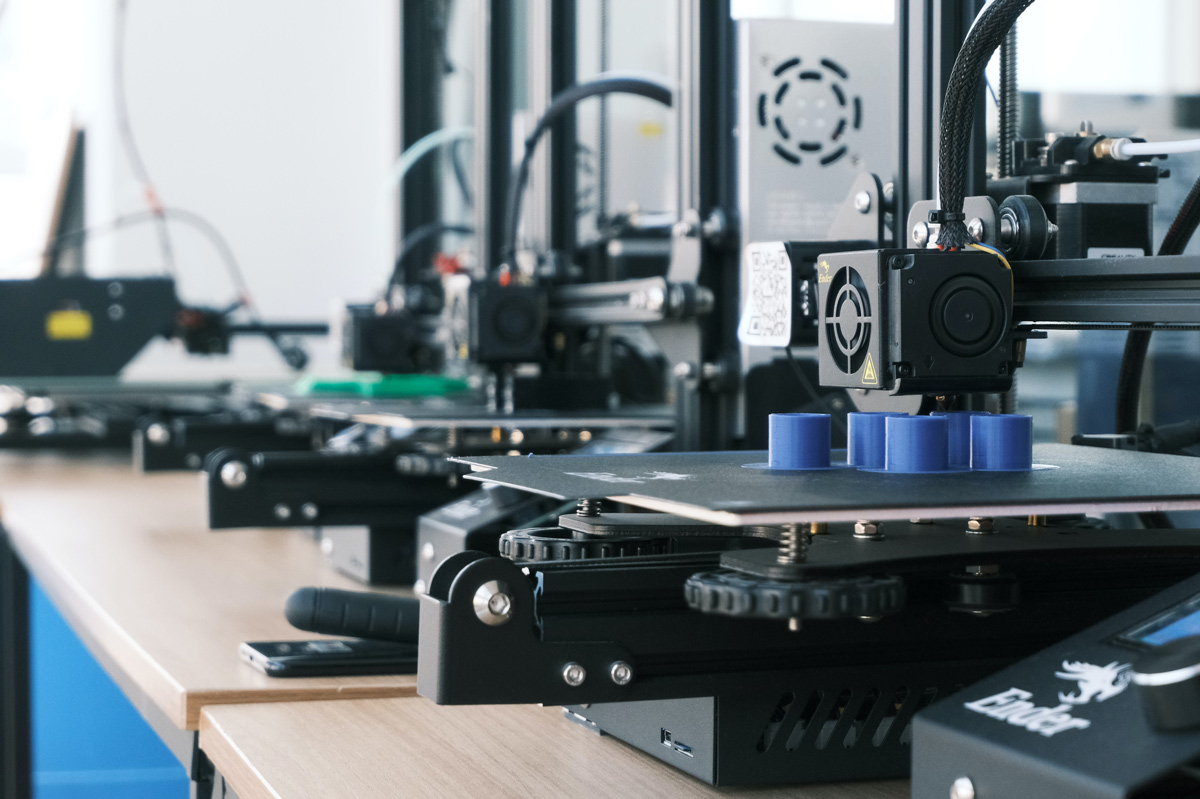
Alternative Buildout Matters
One of the wonderful specters we see in retail over and over again is a willingness to be flexible, to switch gears, and to change directions in order to keep moving forward. It’s one of the most invigorating reasons to be in this industry. There are many creative and innovative options rising to the forefront to make it easier to complete construction as expected.
“Just as we’ve seen new store formats or logistics solutions in response to the pandemic, businesses are becoming more adaptable and flexible overall in response to a new normal. Those that are prepared to make the most of this will benefit in the long run if any other supply chain issues arise.” said Tom McGee, president and CEO of ICSC, in an interview with Costar.
Some of the alternatives being considered include:
3D Printing
3D printing is becoming an innovative way forward in retail design construction. There have been entire buildings manufactured from 3D printing, and it’s offering retailers who need to open sooner a way of moving forward without losing all the elements of their design. According to Construction Dive, 3D printing is more cost-effective and projects can be completed much more quickly.
Using Different Materials
Even though lumber prices are starting to fall, the overall cost of construction remains higher than expected. Many retailers are seeking out alternative materials to be able to complete their projects, whether for construction or for interior design elements.
Local Sourcing
There has been an increase in demand for materials manufactured in the U.S. in order to shorten the supply chain. While this may not be a permanent solution to the issue, in the short-term, it allows construction to move forward with both construction.
Prefab
Robins & Morton makes the argument for prefabrication to ease the supply chain issues, reduce costs, and overcome labor shortages: “Once dismissed by skeptics as a risky idea destined to diminish construction quality, prefabrication is now universally embraced as an industry best practice. Companies in all building sectors are investing in it, clients are intrigued by its savings potential, and the field staff is integrating it in ways that will forever change the traditional supply chain in construction.”
Using Existing Construction
Not only can it be cost-effective to use an existing building and transform it for your brand, but it can ensure you get the location you want. Demand for prime locations is growing rapidly but given the cost and delay in constructing an entire storefront, the investment in retrofitting an existing location can be worthwhile. It can even be inspiring.
At the end of the day, suggests Seitz, you have to set the tone early and understand the client’s priorities. Then use your experience to develop forward-thinking design that is flexible enough to withstand the current industry climate.